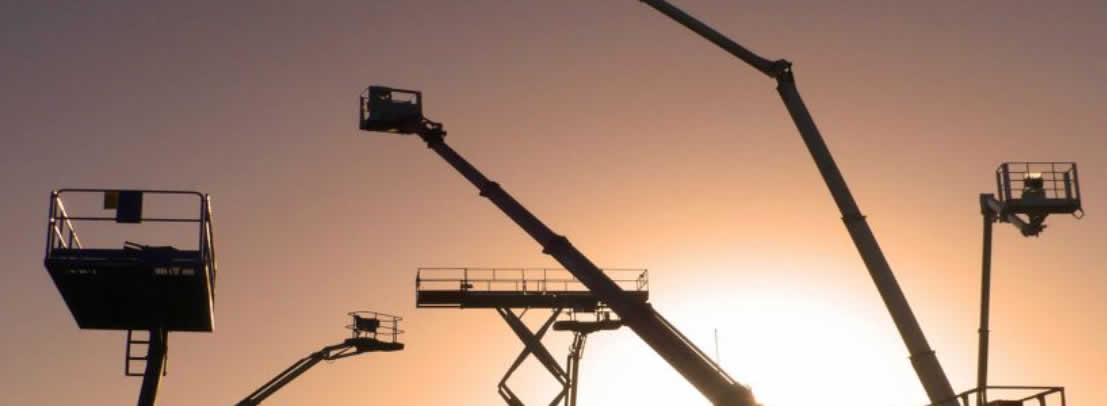
Before an operator begins to use a MEWP, he should carry out a static pre-use inspection to ensure that it is structurally safe and has no faults that could put themselves or others at risk.
Pre-use checks are identified in the manufacturer’s operators manual, which should be supplied with the MEWP. Carrying out pre-use checks will help identify that the MEWP has not suffered from any vandalism, abuse, impact damage or wear and tear that could present a safety issue.
Are the wheels and tyres in good condition, have the batteries been charged, is there sufficient fuel, is there any damage? These are all important points that a pre-use check will cover.
Pre-use checks are not complicated and should only take about 10 to 20 minutes, depending on machine size and complexity. As well as promoting best practice, regular pre-use checks will reduce the likelihood of accidents and breakdowns.
IPAF have made the following comments and recommendations about pre-use checks:
Before use each day or at the beginning of each shift, the aerial platform shall be given a visual inspection and functional test including, but not limited to, the following:
- Current in-service inspection
- Operating and emergency controls
- Safety devices
- Personal protective devices
- Air, hydraulic and fuel systems
- Engine cooling systems, water, engine oil and hydraulic levels
- Cables and wiring
- Loose or missing parts
- Tyres, wheels and brakes
- Placards, warnings, control markings and operating manuals
- Outriggers, stabilisers, and other structures
- Guardrail system
- Items specified by the manufacturer
Following a pre-use check, the operator should conduct a full function check of the MEWP to ensure that it operates correctly. Once this has been confirmed, then the emergency lowering system should also be confirmed to be fully functional.
If you have any queries about pre-use checks please contact us on 01279 501501.